介紹一下P20模具鋼的鍛造工藝
P20模具鋼是美國等級,是預硬化塑料模具鋼的一種,相當于中國等級3Cr2Mo。P20模具鋼淬透性高、綜合力學性能好、硬度均勻、拋光性能好,更適合制造形狀復雜的大中型精密模具,在世界范圍內得到了廣泛應用。
結合設備情況及鋼種特點,生產工藝流程如下:鐵水→脫硫→轉爐→吹氬→LF爐→RH爐→連鑄→熱送→加熱→脫磷→軋制→矯直、冷床風冷→剪切、表面檢驗→探傷→回火→檢驗、標記、入庫。鍛造P20模具鋼時注意以下幾點:
1.煉鋼過程控制
1)嚴格控制雜質含量。模具鋼中的夾雜物,尤其是硬脆夾雜物,會嚴重降低鋼的拋光性能。鋼中硫含量的增加會增加其腐蝕不均勻性,直接影響塑料模具表面圖案的蝕刻性能,因此鋼中硫含量應控制在0.01%以下。
2)控制氫氣和氮氣的含量。在鋼從液相轉變?yōu)楣滔嘁约半S后的冷卻過程中,氮和氫的溶解度急劇下降。除了凝固時的偏析,殘余的氮氣和氫氣會超過溶解度極限,析出氣體,容易產生氣孔。這些氣孔破壞了鋼材的連續(xù)性,降低了探傷合格率。此外,鋼中的碳在高溫下與高壓氫氣反應生成甲烷,其壓力也會促使裂紋產生,也會降低探傷合格率。
3)控制中心隔離。合金模具鋼含碳量和合金量高,導熱性差。在板坯凝固過程中,柱狀晶發(fā)展,容易形成中心偏析。鋼板切割時,中心偏析部分由于熱淬火而發(fā)生結構轉變,在熱應力和結構應力的共同作用下,容易沿中心偏析部分開裂。此外,中心偏析導致模具性能波動,容易出現(xiàn)模具加工過程中拋光質量差、變形大的問題,更終導致模具無法滿足用戶的要求。
針對上述控制要求,我們采取了以下控制措施:保證助焊劑和輔料干燥;氧槍、煙罩、LF爐無漏水現(xiàn)象;Rh真空處理時間不小于25min,軟吹時間不小于8min;;采用保護澆注,中間包鋼水過熱度控制在30℃以內;確保連鑄機設備狀況良好,采用輕壓下技術。
2.軋鋼過程控制
1)加熱
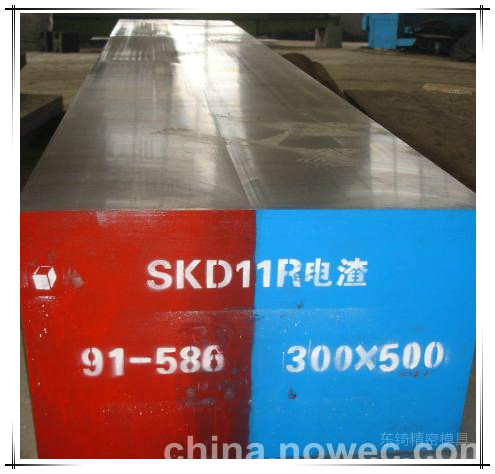
連鑄坯采用熱送熱裝,含碳量和合金量高,導熱性能差。加熱時,應控制加熱溫度和時間,避免鋼坯斷裂和脫碳。
板坯加熱溫度要求如下:預熱段不超過800℃,加熱段1050~1150℃,第二加熱段1200~1240℃,均熱段1200~1260℃,加熱時間至少控制在1min/mm。
2)軋制和冷卻
鋼板應在不低于1050℃的起始溫度和不低于950℃的終軋溫度下用立式輥軋制,軋制后空冷。為保證鋼板的平直度,前兩道次應適當降低壓下量,后兩道次應適當降低澆鑄速度,軋制后矯直1~3道次的矯直溫度不應低于450℃。錳、鉻、鉬等合金元素的加入擴大了奧氏體區(qū),降低了Bs點,提高了過冷奧氏體的穩(wěn)定性,延緩了其轉變,但延遲珠光體轉變的效果遠大于延遲貝氏體轉變,導致珠光體和貝氏體轉變曲線的分離,使貝氏體轉變更加突出,從而大大提高了貝氏體的淬透性,即使在空冷狀態(tài)下也能獲得全斷面貝氏體組織。
由于該鋼種熱應力敏感性高,鋼板應堆放冷卻或放入箱內緩冷48h以上。
3.熱處理和檢驗
軋制鋼板斷面洛氏硬度試驗結果見表2。對軋制鋼板的金相組織進行了測試。軋制鋼板基體的金相組織為粒狀貝氏體,中心偏析區(qū)為帶狀組織。由于合金元素偏析,中心的帶狀組織難以刻蝕,呈現(xiàn)白色和明亮的顏色。
對軋制鋼板的回火工藝進行了試驗?;鼗饻囟葹?20℃、540℃、560℃、580℃和600℃,回火時間為2h。回火后,測試鋼板的洛氏硬度。在520~600℃回火時,鋼板的洛氏硬度降低,而在560~600℃回火時,鋼板的硬度值相同。檢驗了回火鋼板的金相組織,顯微組織為回火貝氏體。因此,回火溫度范圍為560~600℃。